Production Process |
Seamless Tube / Pipe
|
'U' Tube
|
Welded Tube / Pipe
|
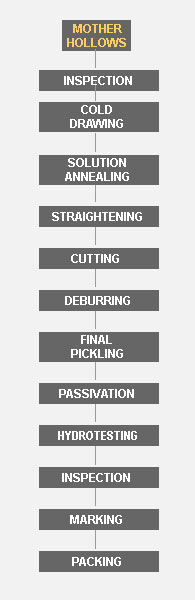
|
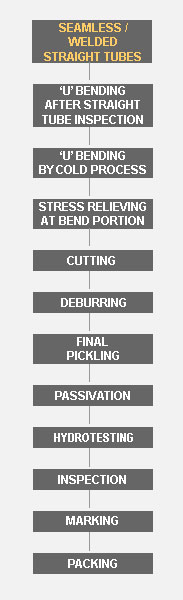
|
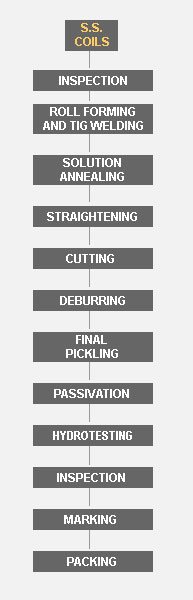
|
|
Grade |
AISI
|
UNS
|
NF
|
EN
|
BS
|
JIS
|
|
|
|
|
|
|
304
|
S30400
|
Z
6 CN 18.09
|
1.4301
|
304
S 15
|
SUS
304
|
304L
|
|
|
|
|
|
316
|
S31600
|
Z
6 CND 17.11
|
1.4401
|
316
S 16
|
SUS
316
|
316L
|
S31603
|
Z
2 CND 17.12
|
|
316
S 12
|
SUS
316L
|
316Ti
|
S31635
|
Z
2 CND 17.12
|
1.4571
|
320
S 17
|
----
|
321
|
S32100
|
Z
6 CNT 18.10
|
1.4541
|
321
S 12
|
SUS
321
|
347
|
S34700
|
Z
6 CNNb 18.10
|
1.4550
|
347
S 17
|
SUS
347
|
|
|
Specifications |
|
ASTM - Standards
|
A
213 / SA 213 |
Seamless
ferritic and austenitic alloy steel boiler, super heater and heat
Exchanger tubes |
A
249 / SA 249 |
Welded
austenitic steel boiler, Super Heater, Heat Exchanger and Condenser
Tubes |
A
268 / SA 268 |
Seamless
and welded ferritic and martensitic stainless steel tubing for
general service |
A
269 /SA 269 |
Seamless
and welded austenitic stainless steel tubing for general service |
A
312 / SA 312 |
Seamless
and welded austenitic stainless steel pipes |
A
358 / SA 358 |
Welded
pipe for High temperature service |
A
688 / SA 688 |
For
Welded feed water heater ‘U’ Tubes |
|
GOST
|
GOST
9940 |
Seamless
stainless steel tubes, hot finished |
GOST
9941 |
Seamless
stainless steel tubes, cold and hot finished |
|
German Standards
|
DIN
17456 |
Seamless
circular austenitic stainless steel tubes for general service |
DIN
17457 |
Welded
circular austenitic stainless steel tubes subject to special requirements |
DIN
17458 |
Seamless
circular austenitic stainless steel tubes subject to special requirements |
DIN
28180 |
Seamless
steel tubes for heat exchangers |
SEW
400 |
Stainless
steels |
AD
2000-W2 |
Materials
for pressure vessels - austenitic stainless steels |
DIN
EN ISO 1127 |
Seamless
stainless steel tubes (Dimensions and weights) |
|
NF Standards
|
NF
A 49-117 |
Seamless
ferritic and austenitic stainless steel tubes for general service |
NF
A 49-217 |
Seamless
ferritic, austenitic, and ferritic-austenitic stainless steel
tubes for heat exchangers |
|
BS
Standards
|
BS
3059 |
Steel
boiler and super heater tubes |
BS
3605 |
Austenitic
stainless steel pipes and tubes for pressure purposes |
BS
3606 |
Steel
tubes for heat exchangers |
|
JIS Standards
|
JIS
G 3459 |
Stainless
steel pipes |
JIS
G 3463 |
Stainless
steel boiler and heat exchanger tubes |
|
|
Pipe Dimension |
|
Size |
Wall Thickness & Weight
|
Nominal
Pipe Size
in inch |
Outside
Diameter |
Schedule 5s
|
Schedule 10s
|
Schedule 40s |
Schedule 80s
|
In mm. |
W.T.
In mm. |
W.T.
kg/Mt. |
W.T.
In mm. |
W.T.
kg/Mt. |
W.T.
In mm. |
W.T.
kg/Mt. |
W.T.
In mm. |
W.T.
kg/Mt. |
1/4 |
13.72 |
1.24 |
0.387 |
1.65 |
0.498 |
2.24 |
0.643 |
3.02 |
0.808 |
3/8 |
17.15 |
1.24 |
0.493 |
1.65 |
0.640 |
2.31 |
0.857 |
3.20 |
1.116 |
1/2 |
21.34 |
1.65 |
0.812 |
2.11 |
1.014 |
2.77 |
1.286 |
3.73 |
1.642 |
3/4 |
26.67 |
1.65 |
1.032 |
2.11 |
1.300 |
2.87 |
1.708 |
3.91 |
2.225 |
1 |
33.40 |
1.65 |
1.310 |
2.77 |
2.121 |
3.38 |
2.537 |
4.55 |
3.282 |
1 1/4 |
42.16 |
1.65 |
1.671 |
2.77 |
2.728 |
3.56 |
3.435 |
4.85 |
4.524 |
1 1/2 |
48.26 |
1.65 |
1.923 |
2.77 |
3.150 |
3.68 |
4.101 |
5.08 |
5.484 |
2 |
60.33 |
1.65 |
2.421 |
2.77 |
3.989 |
3.91 |
5.515 |
5.54 |
7.588 |
2 1/2 |
73.03 |
2.11 |
3.741 |
3.05 |
5.336 |
5.16 |
8.756 |
7.01 |
11.570 |
3 |
88.90 |
2.11 |
4.578 |
3.05 |
6.546 |
5.49 |
11.449 |
7.62 |
15.484 |
3 1/2 |
101.60 |
2.11 |
5.258 |
3.05 |
7.514 |
5.74 |
13.756 |
8.08 |
18.891 |
4 |
114.30 |
2.11 |
5.981 |
3.05 |
8.483 |
6.02 |
16.298 |
8.56 |
22.628 |
5 |
141.30 |
2.77 |
9.593 |
3.40 |
11.721 |
6.55 |
22.065 |
9.52 |
31.364 |
6 |
168.28 |
2.77 |
11.461 |
3.40 |
14.014 |
7.11 |
28.648 |
10.92 |
43.142 |
8 |
219.08 |
2.77 |
14.979 |
3.76 |
20.240 |
8.18 |
43.129 |
12.70 |
65.526 |
10 |
273.05 |
3.40 |
22.920 |
4.19 |
28.163 |
9.27 |
61.131 |
12.70 |
82.661 |
|
|
Tube Dimensions |
Wall thickness
in mm. |
0.5 |
0.6 |
0.7 |
0.8 |
1.0 |
1.2 |
1.6 |
2.0 |
2.6 |
3.0 |
3.2 |
3.6 |
O.D.
in mm. |
Weight in kg/meter |
6.0 |
0.069 |
0.081 |
0.093 |
0.104 |
0.125 |
0.144 |
0.176 |
- |
- |
- |
- |
- |
9.52 |
0.112 |
0.134 |
0.154 |
0.174 |
0.213 |
0.249 |
0.317 |
- |
- |
- |
- |
- |
10.0 |
0.119 |
0.141 |
0.163 |
0.184 |
0.225 |
0.264 |
0.336 |
- |
- |
- |
- |
- |
12.7 |
0.153 |
0.182 |
0.210 |
0.238 |
0.293 |
0.345 |
0.444 |
- |
- |
- |
- |
- |
14.0 |
0.169 |
0.201 |
0.233 |
0.264 |
0.325 |
0.384 |
0.496 |
- |
- |
- |
- |
- |
15.87 |
0.192 |
0.229 |
0.266 |
0.301 |
0.372 |
0.440 |
0.571 |
0.694 |
- |
- |
- |
- |
19.0 |
0.231 |
0.276 |
0.320 |
0.364 |
0.450 |
0.534 |
0.696 |
0.850 |
1.066 |
1.200 |
1.264 |
- |
25.0 |
0.306 |
0.366 |
0.425 |
0.484 |
0.600 |
0.714 |
0.936 |
1.150 |
1.456 |
1.650 |
1.744 |
1.926 |
25.4 |
0.311 |
0.372 |
0.432 |
0.492 |
0.610 |
0.726 |
0.952 |
1.170 |
1.482 |
1.680 |
1.776 |
1.962 |
31.8 |
- |
- |
- |
- |
- |
0.918 |
1.208 |
1.490 |
1.898 |
2.160 |
2.288 |
2.538 |
38.0 |
- |
- |
- |
- |
- |
1.104 |
1.456 |
1.800 |
2.301 |
2.625 |
2.784 |
3.096 |
44.5 |
- |
- |
- |
- |
- |
1.299 |
1.716 |
2.125 |
2.724 |
3.113 |
3.304 |
3.681 |
50.8 |
- |
- |
- |
- |
- |
1.488 |
1.968 |
2.440 |
3,133 |
3.585 |
3.808 |
4.248 |
63.5 |
- |
- |
- |
- |
- |
- |
2.476 |
3.075 |
3.959 |
4.538 |
4,824 |
5.391 |
76.1 |
- |
- |
- |
- |
- |
- |
2.980 |
3.705 |
4.778 |
5.483 |
5.832 |
6.525 |
101.6 |
- |
- |
- |
- |
- |
- |
4.000 |
4.980 |
6.435 |
7.395 |
7,872 |
8.820 |
|
|
'U' Tube |
'U' bending is done by
cold working process.
'U' bending is done to
the required radius as per customer drawings.
The bend portion and six
inch leg is stress relieved by resistance heating.
Inert gas (Argon) is
passed through it at the required flow rate to avoid oxidation in ID.
The radius is checked
for its OD and wall thinning with the recommended specification.
The physical properties
and microstructure is checked at three different position.
Visual inspection for
waviness and cracks is done with Dye Penetrant Test.
Each tube is then hydro
tested at the recommended pressure to check for leakage.
Cotton ball test is done
to check the ID cleanliness of the tube.
Thereafter pickled,
dried, marked and packed.
All procedure is
strictly followed as per TEMA "C" and ASTM A-688.
|
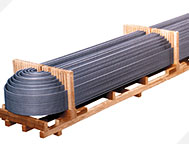
|
|
Bead removal Tube |
Bead removal is done as
per the requirement of standard specifications.
Bead is cold worked and
brought in level with the base metal.
Bead rolling is made
in-line before heat treatment on tube mill.
Weld structure will
thereby recrystallise & homogenize faster in annealing process.
Which improves corrosion
resistance.
Which improves easy
expansion in tube sheets and orbital welding.
Which
improves easy flow and easier cleaning and less scale deposits. |
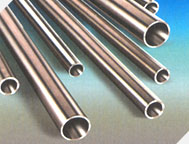
|
|
품질관리 |
All products of Suraj
Stainless Ltd.' have to meet a very high standard, set by stringent quality
specifications and norms. All process parameters and conditions are developed
and constantly monitored throughout the entire manufacturing process.
A quality system to ISO
9001 : 2000 , AD 2000 – Merkblatt / WO , and PED – 97 /23/EC as outlined in
this manual has been developed and implemented to ensure that all the customer requirements
is satisfied. The quality system is applicable to all departments and all
activities undertaken by the company for manufacturing of Stainless Steel
Seamless/Welded Pipes, Tubes and ‘U’ Tubes.
The quality policy of Suraj
Stainless Ltd is very simple to perform work of the highest attainable quality
in accordance with applicable codes / standards / specification and customers
specification. Our products are subjected to various quality testing such as
Eddy Current test, Hydrostatic test, UTS, Hardness test, Air under water test,
Dimensional test, visual test etc.
Quality Control measures
include chemical analysis, measurement of mechanical and metallurgical properties
and close dimensional tolerances as per applicable codes / standards /
specification.
|
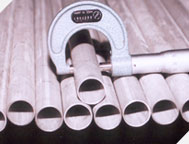
|
|
Quality Assurance Process
|
Quality Assurance Process
|
Sr. No.
|
Process Operation
|
Quality Characteristics
|
Method of control
|
Test equipments
|
01. |
Raw Material (Strip,
Mother-Hollow) |
a) Dimension b) Chemical Analysis
c) Control of Slit Width within Specified limits d)
Surface |
Actual measurement as per Std. Analysis
of all elements as per Std. Testing as per various Std, Actual
measurement of width, thickness & recording, Visual
Inspection. |
Vernier, Micrometer Volumetric &
Gravimetric, UIN 10-T Testing Machine Brinnels/Rockwell
Tester |
02. |
Tube Mill |
a) Weld Test, Flare Flange,
Flattering Reverse bend & Reverse Flattening b) Inspection
of Weld, Seam c) Dimensions d) Surface |
Testing as per Standard specification
& recording the results. One test for every 30 to 35 mtrs. Visual
Inspection Weld zone fusion of O.D. Thickness & Length. Check
roller surface profile & finish. |
Universal testing Machine UIN 10-T
Self Fabricated Tube Mill
Microscope & Visual. Vernier,
Micrometer & Measure Tape. |
03. |
Cold Drawing |
OD WT Surface finish
on OD&ID Length. |
Dimension Measurement Visual
Inspection |
Micrometer
Measurement
Tape |
04. |
Oxalate Soap Coating |
Bath analysis Temperature |
Bath Testing Scratch
Test |
Volumetric
Analysis Thermo-meter |
05. |
Solution Annealing |
A) Temperature b) Hardness c)
Micrometer |
Automatic Relay Temp/Controller Adjusted to present
level. Measurement of Hardness as per Std one Test / Lot /
Heat |
Digital graphic Temperature
Scanner Recorder Digital Temperature Indicator and
control metallurgical Microscope Rockwell / Brinell. Hardness
tester. |
06. |
Straightening |
Straightness OD Surface |
Adjust roller setting measure
Visual |
Roller straightening m/c Straightness
edge/keep on table Micrometer Visual Observation |
07. |
Cutting |
Square cut
Length |
Right angle to
length Visual |
Abrasive cut-of
m/c MessureTape |
08. |
Deburring |
Burs removal OD, ID
Edges |
Visual |
Pneumatic/
electrical Deburring tool Check with hand/visual |
09. |
Chemical Treatment a) Pickling b)
Passivation |
Concentration Concentration Temperature |
One Test / Bath
Day One Test / Bath Day Temperature Control |
Hydraulic
Tester. Volumetric Analysis Thermometer. |
10. |
Hydraulic Test |
Test Pressure |
100% Inspection at
test pressure specified as per Standard. |
Hydraulic
Pressure tester |
11. |
Eddy Current Test |
Surface / Sub
Surface defects |
As per
Standard. |
Eddy Current
Test Instrument |
12. |
Final Inspection |
IGC
Test Dimensions Surface Physical Testing Grade Check Prod.
Analysis |
As per
standard 100% inspection of Dimensions as specified. Visual inspection
for surface defects. Physical Testing as per standard
specification. (100% Inspection) Chemical Analysis.. |
Beaker,
Condenser, Chemicals, hot Plate, Micrometer / Vernier
Universal
testing M/c. UIN-40T Molly detector & carbon sampling at random
spectro / wet method. |
13. |
Marking |
Marking as per
Std. |
Check for
proper marking |
InkJet Machine/Electro
ETCH Co-relation of Heat No. Size, Grade, etc. With Test
Certificate. |
14. |
Packing |
Seaworthy
packing Box crate Bundles Fumigated. |
Check for packing,
quantity, shipping mark, fumigation certificate. |
Box, Crate,
Polythene, Hessian. |
|
List of Testing Equipments |
Universial testing machine |
Capacity |
40 tons |
Make |
F.I.E. |
Facility |
i)
Computerised with printer ii) Calibrated by third party |
No. of Machines |
One |
|
Hardenss Tester |
Make |
Saroj |
Facility |
Hardness tester with superficial facility to measure
hardness in HRC, HRB, 15T, 30T Scale
|
|
Polishing / Grinding
Machine
|
Single 200 mm diameter disc
polisher with variable speed facility for grinding &
polishing
|
|
Eddy Current Testing
|
Make |
Technofour, Pune
|
Facility |
Digital Flawmark Electronics Test
Systems
|
|
|
|
|
Chemical Testing
Laboratory
|
Facility to carry out day-to-day testing of
different solution used in packing
department.
|
|
|
|
Certificates |
ISO9001:2000ANSI/ISO/ASQ Q9001 |
|
AD2000Merkblatt W0 |
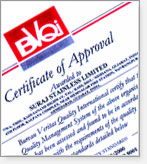
|
|
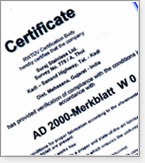
|
PED97/23/EC
|
|
Government Export House
|
|
Awards for Export Excellence
|
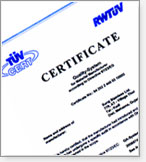
|
|
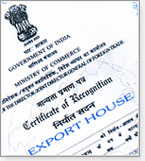
|
|
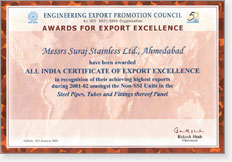
|
|
|
Packing & Transportation Method |
As per client's
requirement, we adopt 3 different ways to pack our goods.
|
Wooden box packing
|
|
Crate packing
|
|
Bundle packing
|
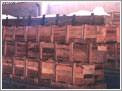
|
|
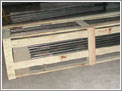
|
|
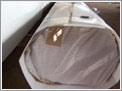
|
|
|
Once the packaging is
done, we transport our goods by following three ways :
|
Open Top Container |
LCL Cargo |
Flat Bed Container |